Horezu Ceramics – UNESCO intangible heritage
Horezu, in Vâlcea County (in southern Romania) is the place where the pottery tradition has been passed down from generation to generation for hundreds of years.
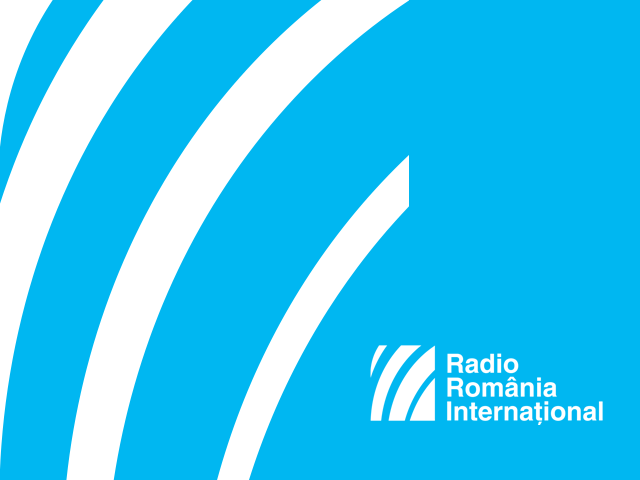
Ion Puican, 02.10.2021, 14:00
Horezu, in Vâlcea County (in southern Romania) is the place where the pottery tradition has been passed down from generation to generation for hundreds of years, pottery being a craft raised to the rank of traditional art. As you drive down the winding roads on the hills that go up from Horezu, you enter Olari Street-a Street full of the houses-workshops of the potters in the area. On both sides of the road visitors are welcomed by house porches crammed with ceramic objects, decorated fences, windows and doors adorned with hanging plates, jugs and cups placed on top of fences – all of them emanating color, joy and centuries-old Romanian tradition. We stopped at the workshop of the master potter Mihai Bâscu, to discuss about this special type of ceramics and about how it is made.
Mihai Bâscu: “When you say Horezu, you actually mean the only locality in Romania with two UNESCO brands – Hurez ceramics and Hurezi Monastery. Hurez ceramics is famous around the world, and its fame is also due to its being included on the UNESCO intangible heritage list, because we have a unique way of decorating ceramics and equally unique decorating tools. The decorating tools we use are the cow horn, the goose and jay feather. As everyone knows, the general symbol of the region is the “Rooster of Hurez”, and we also have some secondary symbols, so to say, such as the “Tree of Life”, the fish, the snake, the sun, the “Spiral of Life”, plus the traditional motifs of the spider or spiral, the ear of wheat, the peacocks tail, the flower, the trefoil, and the vortex. Our decorations are a combination of traditional motifs, of motifs and symbols, or just of symbols.”
The Horezu ceramic objects are quite varied, ranging from small to big-size objects. Mihai Bâscu has described their range: “The Hurez ceramics includes objects and especially plates starting from the size of 8 centimeters up to 40 centimeters. In this regard, I can assume the merit of making a ‘revolution’ in the years 2000, which made a difference from the ceramics of my father’s generation, the so-called ‘golden generation’, as I made the biggest Horezu objects, plates and even large soup bowls. In addition, Horezu ceramics also includes cups, brandy cups and “square” plates. We have diversified the range, making magnets and even clay sinks.”
Potter Mihai Bâscu told us how he learned this craft and talked about the secrets of this traditional profession: “This craft is passed down from father to son. I learned it as a child, I also learned the old technology, as I used to help my father, by preparing the clay. At the time, since there were no electric engines, I would prepare the paints by stirring with my hand. The clay we use is from our area, from Dealul Ulmului — Ulmului Hill, where I usually go in autumn to take clay for a whole year. I take a bulldozer to dig 2 meters until I find the good clay, and then, helped by some of the villagers, I pick the best clay and clean it. I bring it home clean, there are also very large lumps. I bring it in a clean trailer. I store it at home and leave it outside all winter — because the freeze-thaw cycle crumbles the clay. I mix the clay twice in the mixer, then I knead it in my hands until it becomes very good for shaping. The paints we use are all natural, from earths I prepare myself. White, orange and black are natural types of earth, and for the green and blue earths I make several combinations. I combine copper oxide and kaolin (white earth) to obtain green, and cobalt and white earth to obtain blue earth. After that, there follow the phases of the work proper: modeling clay, in the sense of shaping the clay into whatever form I want, a plate, a bowl or a cup. The second phase is decoration — which is the most spectacular and important phase in our technology. The object is decorated in a fresh form, as we call it, fresh but hardened, because, the paints being made of earth, the new decoration merges into the clay object. Then, because our objects, 70-80%, are hanged on walls, I scrape them on the back, make a hole for hanging and, what is very important, I stamp them with my name. Then I put them to dry. When they are perfectly dry, they enter the first firing in the oven, which lasts about 8 hours, at a temperature that reaches 850 degrees. The next day I take them out of the oven, apply enamel on them and give them a second firing at 1,020 degrees. This is how a final object is obtained.”
In the end of our discussion, the master potter Mihai Bâscu wanted to add something which he learned from his father and which refers to the ruler of Wallachia Constantin Brâncoveanu (1654-1714), who was canonized as a holy martyr. Brâncoveanu was the founder of many churches and monasteries, a leader under whose rule the Romanian arts and culture knew an extraordinary development:
Mihai Bâscu: “What I didn’t tell you, something very important — is something that I know from my father: pottery in our region has been a craft since the time of the ruler Constantin Brâncoveanu. His second passion after the church was pottery, we even have a decoration style called Brancoveanu decoration style.” (LS)